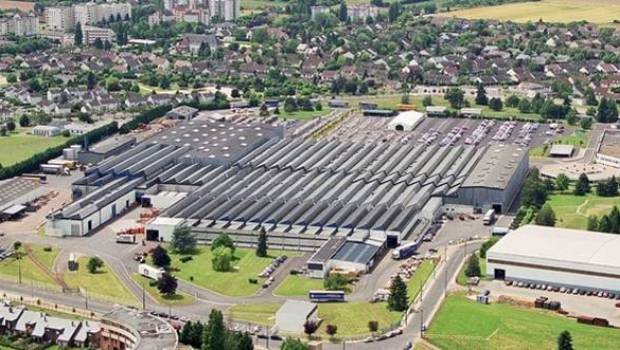
L’Américain Otis mise sur la France plutôt que de délocaliser
Non loin de la faïencerie de Gien, dans le Loiret, l’américain Otis produit des ascenseurs de toutes dimensions. Le siège vient de décider d’investir en France, et non en Tchéquie ou en Espagne.
L’arche en bardage détonne un peu dans le paysage verdoyant de Gien (Loiret). Les deux tours culminent à 66 mètres de hauteur, dominant cette petite ville des bords de Loire. De quoi tester des ascenseurs dans des gaines comparables à celles d’un immeuble de grande hauteur.
À l’est et à l’ouest, se découpent les silhouettes des deux centrales nucléaires de Belleville-sur-Loire et de Dampierre. Plus près, le regard plonge vers un établissement militaire de maintenance des chars Leclerc. Là-bas, près du château, la faïencerie de Gien maintient la tradition de la ville. Au pied des tours, 42 000 m2 d’atelier.
C’est ici que l’américain Otis fabrique les ascenseurs de l’Europe du Nord, notamment ceux de la France, où Otis est leader, de l’Allemagne et de la Suisse. Avec 630 salariés, dont une moitié d’ouvriers, à une heure et demie de Paris, Otis est la dernière usine française d’ascenseurs, depuis la fermeture de ThyssenKrupp il y a deux ans, à Angers.
Retour en haut de la tour. Des panneaux photovoltaïques et une modeste éolienne coiffent l’édifice. De quoi alimenter quatre batteries dissimulées dans la gaine d’ascenseur et l’affranchir du courant triphasé. Le premier ascenseur de ce type a été mis en place il y a deux ans, à Rezé en Loire-Atlantique. Plus de deux mille se sont vendus depuis, essentiellement en Europe du Sud.
« La puissance d’un sèche-cheveux »
« 500 watts suffisent, c’est-à-dire la puissance d’un sèche-cheveux, alors qu’il fallait 3 000 à 5 000 watts auparavant, explique Christophe Durand, ingénieur d’essai. Les batteries fournissent les pointes d’énergie. La récupération du freinage représente 40 % de l’électricité. »
Les fondamentaux de l’ascenseur n’ont pas changé depuis l’invention du parachute d’ascenseur par l’Américain Elisha Graves Otis, en 1853, à New York. La tour de Gien teste toujours les mâchoires disposées le long de la cabine qui serreront la courroie en cas de descente trop rapide : un dispositif dans la poulie, située en haut de la tour, est alors déclenché par la force centrifuge et contracte les mâchoires en acier.
Ce qui a changé, dernièrement, c’est que les câbles ont laissé la place aux courroies, faites de minces torons d’acier noyés dans un ruban de polyuréthane. Fini le graissage et le bruit pour les occupants des appartements. Fini, aussi, les machineries volumineuses et les mètres carrés perdus. Un argument massue pour les clients d’Otis, qui sont les promoteurs des immeubles.
Une fois réglées l’alimentation et la sécurité, reste à réussir le plus dur : concevoir et fabriquer un assemblage de 20 000 pièces qui doit s’adapter à des situations innombrables. C’est le travail de l’atelier, d’où sort un ascenseur toutes les vingt minutes et une porte palière toutes les quatre minutes. Le travail des commerciaux et des techniciens de la maintenance également, qui chez Otis forment le gros de la troupe : « Sur 63 000 salariés d’Otis dans le monde, seuls quelques milliers travaillent exclusivement dans les usines, souligne Fabienne Loréal, la directrice de l’usine de Gien. La majorité des salariés se trouvent au plus près de nos clients, dans les régions, à entretenir les ascenseurs, à les monter et à les vendre. »